What new processes need to be added to wine boxes to attract consumers?
- Share
- Issue Time
- Feb 21,2025
Summary
In today's highly competitive market, wine box design needs to do more than just protect the product; it must also capture consumers' attention through innovative craftsmanship and design, enhancing brand image and adding value to the product.
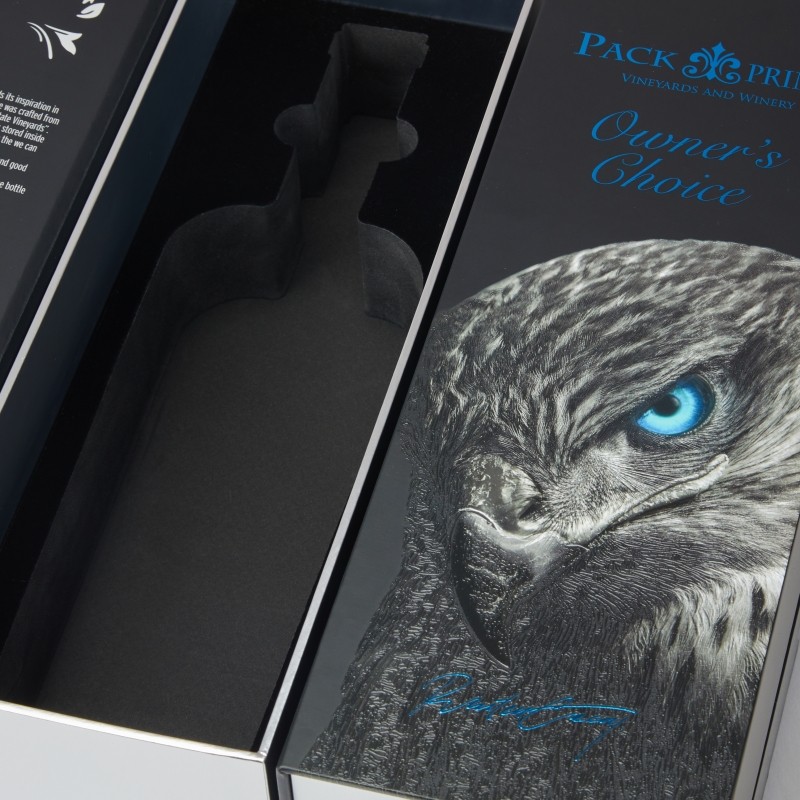
Although many traditional techniques, such as hot stamping, embossing, and UV coating, are already used in wine box design, there are still some shortcomings. Traditional wine boxes often lack a sense of depth and texture, offering a rather uniform tactile experience. High-end tactile techniques, such as Scodix, can be introduced to create raised textures, combine matte and gloss finishes, and add intricate patterns, giving consumers a unique, luxurious tactile sensation when handling the packaging and elevating the product's sense of luxury.

Compared with the traditional screen UV process and the Scodix digital UV process:
First, the difference in brightness: The brightness level of the traditional screen UV is usually 60-70GU, while the brightness level of the Scodix digital UV can reach up to 99GU, which is crystal clear like water drops dripping on the printing surface;
Second, the difference in brightness durability: The traditional screen UV is prone to oxidation and yellowing over time, while the Scodix resin ink remains crystal clear after several years;
Third, the difference in the fineness of the expression means: The fineness of the UV scraped out by the traditional screen UV is limited by the plate making precision, and the expression is not fine enough. The Scodix digital UV has different densities and gradient expressions, which can well simulate the veins, borders and other textures of plants;
Fourth, the height difference: In the Braille printing mode, the Scodix digital UV can reach up to 250 microns in one molding, which is beyond the reach of the traditional screen UV process.
Comparison of hot stamping processes:
Hot stamping processes are often used on company logos, texts and other content, giving products a luxurious and high-end feel. From the production process to the display characteristics, the hot stamping of Scodix is different from both hot stamping and cold stamping. In terms of temperature, the hot stamping of Sigodi is maintained at a temperature of 30-40 degrees from the laying of glue to the pasting of electroplated aluminum to curing, which is more like "warm stamping". Let's take a look at the difference between hot stamping and cold stamping compared to hot stamping.
Compared with traditional hot stamping, hot stamping has high brightness and lasting color. The reason is that in the traditional high-temperature hot stamping process, the hot stamping film is at a temperature of more than 100 degrees, and the electroplated aluminum foil will be oxidized to varying degrees and lose brightness. At the same time, affected by the paper texture, the metal texture of the electroplated aluminum is diffusely reflected on the uneven substrate; while at the temperature of 30-40 degrees used by the Scodix hot stamping, the metal coating layer of the electroplated aluminum foil does not undergo a serious oxidation process, and the Scodix ink fills the fine texture of the paper, and the metal texture of the electroplated aluminum is reflected in the form of mirror reflection on a completely flat substrate. The combination of the two makes the Scodix hot stamping particularly shiny.
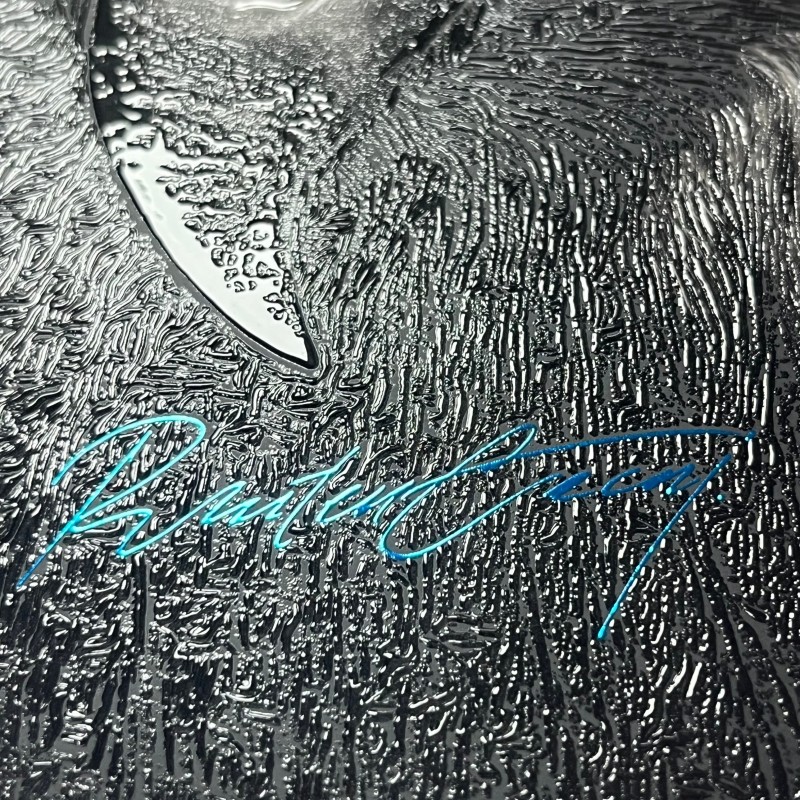
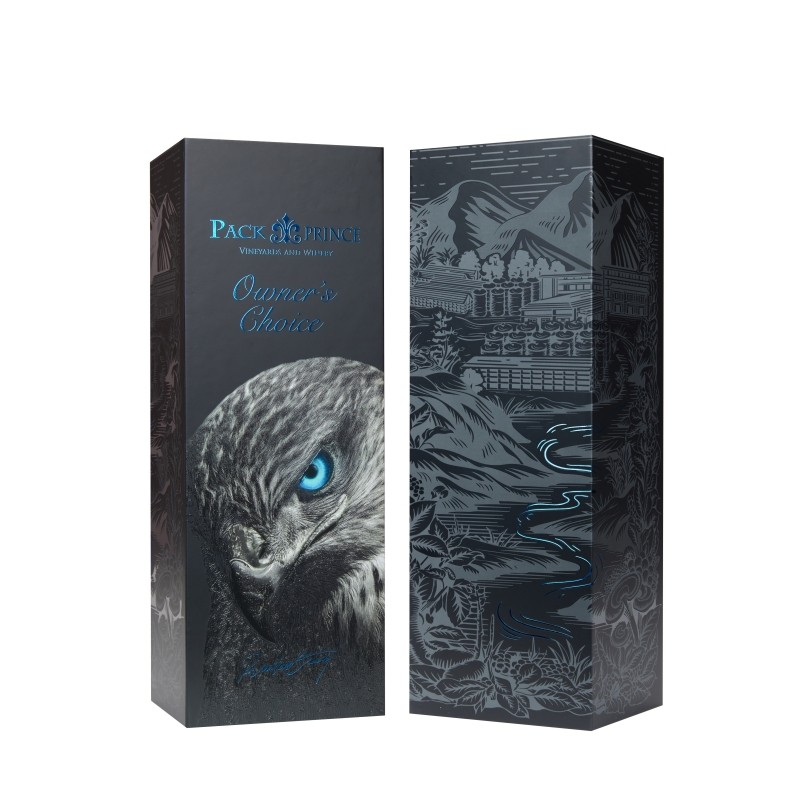
In terms of the durability of brightness, affected by high-temperature oxidation, the packaging boxes of traditional hot stamping technology have problems such as hot stamping falling off and oxidation blackening after being stored for half a year or more. These phenomena directly lead to a series of problems such as the depreciation of the products inside and the impact on the brand image, which is particularly serious for luxury goods. However, the products of the Scodix hot stamping technology have a long-lasting brightness and are not easy to fall off.
Comparison of embossing processes:
The embossing of Scodix is a bulge stacked by UV varnish. There is no depression on the back of the printed sheet, and the hardness is very high after UV curing. This advantage is very important for high-end mounted board gift boxes. There is no need to fill the depression on the back, which can improve efficiency; the back is flat and not easy to bubble, which can greatly improve the yield rate of the mounted board; and with the changes in time, temperature and other environmental conditions, the embossed surface remains flat and stylish, and there will be no surface collapse and pits.
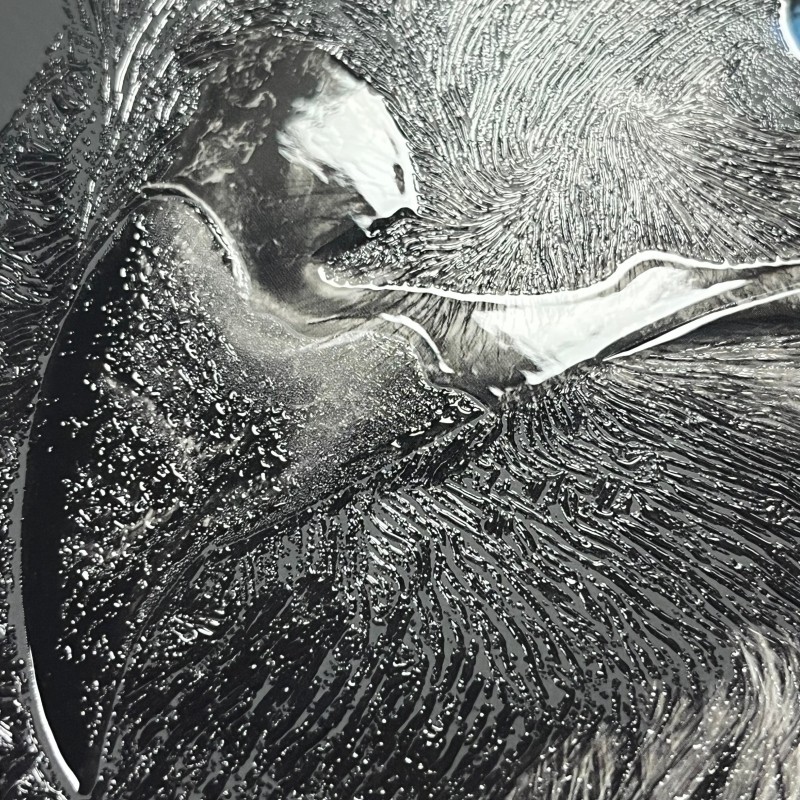
Currently, DHP Factory has integrated this new technique into the design of wine packaging boxes. The effects achieved with the Scodix technology are significantly superior to those of conventional UV coating, hot stamping, and embossing. This technology is now highly mature and has gained substantial popularity in both the European and American markets. It not only enhances the corporate and brand image but also makes the packaging more attractive, highlighting the quality and value of the product.